MRP (Material Requirement Planning)
MRP function in SAP ERP/MES software:
The MRP function maintains the optimal production plan for diverse product manufacturing processes into a smooth flow. This support replaces informal production planning with a structure that uses data from a variety of sources to create an accurate picture of production processes and supply chains. It is important that the planning requirements can be optimized for machine capacity.
Data sources include:
- Material norms
- Does the data exist?
- Inputs from production orders and purchases
- Demand from orders and forecasts
Using the MRP function, the identification of timeline, inventory and data source can be considered in the plan. SAP ERP/MES can use this data to suggest issues related to the materials we need, what we need, how much we need and when we need resources. When these proposals are evaluated, it is possible to create the production orders and purchases necessary to produce the final product with a defined production time. This will be considered for all component and source product requirements.
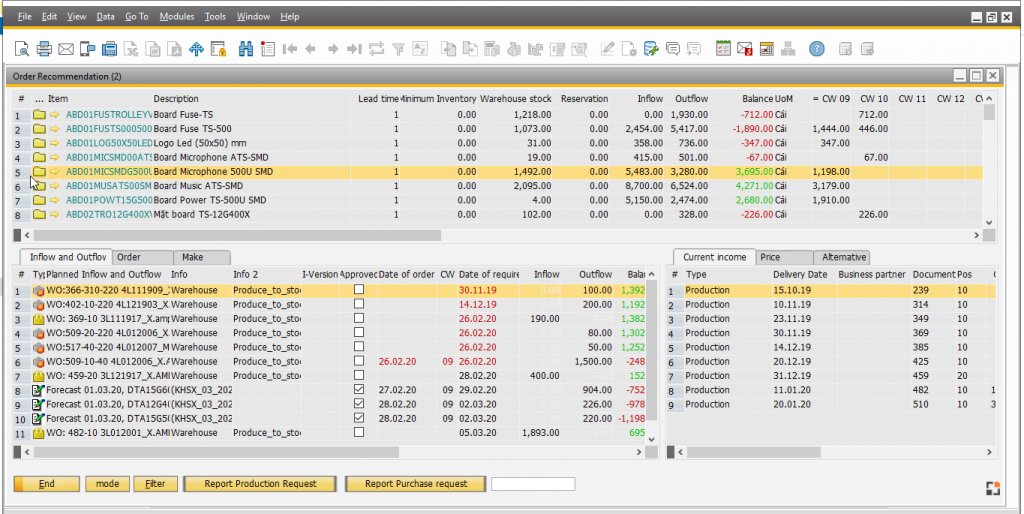
SAP ERP/MES also helps to purchase products that do not have a prediction based on minimum and maximum materials, done through the warehouse.
SAP ERP/MES MRP is managed through an interactive program supporting users.
This allows users to define five-step planning scenarios and demand forecasts based on forecasts. Production Resource Planning (MRP) in SAP ERP/MES generates purchase and production orders based on the current transaction status in the system.
MRP basically works like a system of experts, determining how much to buy for an item and how much to produce for an item at a specific time.
This allows automatic creation of production requests and orders based on the proposal reports. If needed, a product can be converted from the production proposal to the outsourcing proposal.
In addition, it is simple to merge individual POs of suppliers into a single order to make the buying process more smooth.
MRP does not automatically place orders but will recommend orders. These suggestions can be modified and changed by the person in charge, who has the knowledge and practical experience about this. For small and medium-sized businesses, this structure helps to balance automation and manual management.
SAP ERP/MES features help you plan and optimize your material needs, including managing and implementing procurement and manufacturing proposals, as well as other exceptions.
To make suitable suggestions. SAP ERP/MES looks at different supplies and needs, including inventory levels, planned production orders, open orders, expected sales orders, forecast orders … as well as data. overall data such as: Standard of raw materials, planned data such as production deadline, minimum inventory level …
MRP helps make clear suggestions, clear recommendations, provides information that you can select, align and align forecast and reality information.
MRP can run whenever used for modeling purposes.
SAP ERP/MES MRP helps reduce human error when users can use information better.
Direct costs are reduced when predicting the minimum number of orders and the number of orders helps users take advantage of discount orders or batch sizes.
Purchasing managers focus on strategic procurement, instead of worrying about inventory.
Reduce safe inventories or multiple POs for an item because warehouse managers and collectors are not connected.